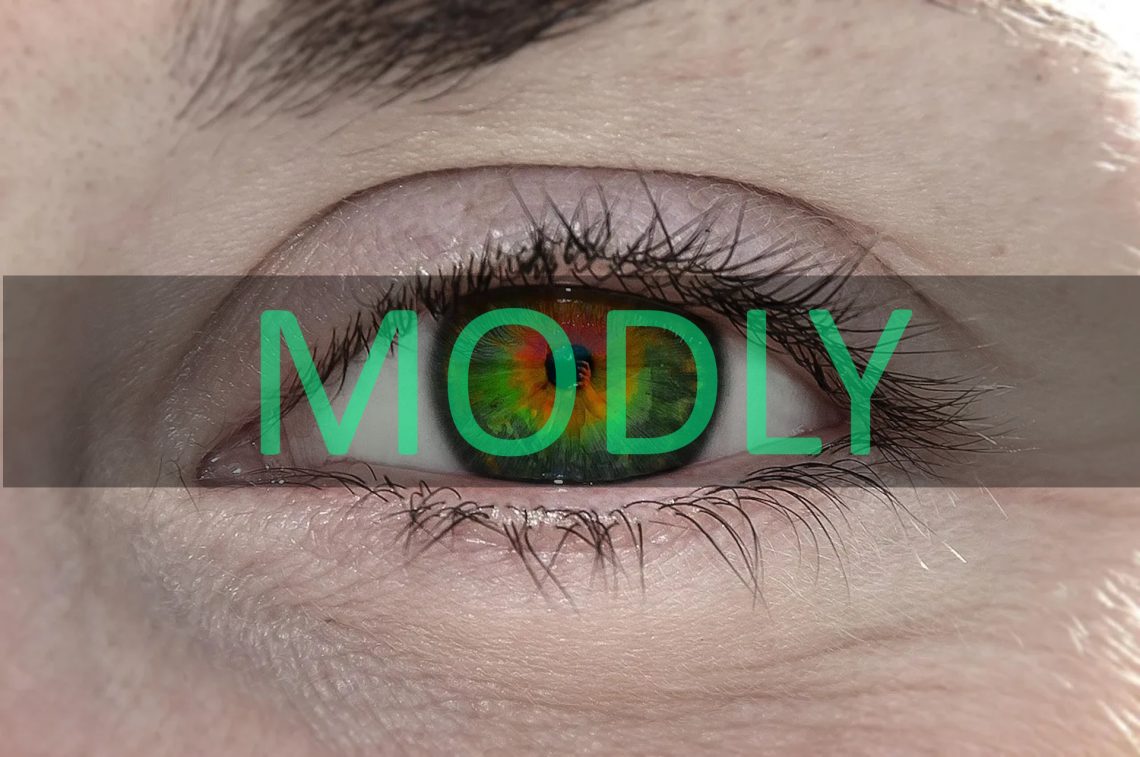
Understanding Flare Nuts: Essential Components for Plumbing and Automotive Use
Flare nuts play a crucial role in various applications, particularly in plumbing and automotive environments. These specialized nuts are designed to create a secure connection between pipes and tubes, ensuring that fluids or gases flow smoothly without leaks. The unique design of flare nuts allows for a tight fit and reliable sealing, making them essential components in systems where pressure and integrity are critical.
Understanding the materials and construction of flare nuts is equally important, as they must withstand varying pressures and temperatures in their respective applications. The choice of materials can affect not only the performance of the flare nut but also the overall efficiency of the system in which they are used.
In addition to their practical functions, flare nuts can also vary in size, shape, and threading, which adds another layer of complexity when selecting the right component for a specific task. Whether you are a seasoned professional or a DIY enthusiast, familiarity with flare nuts is indispensable for anyone working with plumbing or automotive systems.
As we delve deeper into the world of flare nuts, we will explore their types, applications, and best practices for installation and maintenance, ensuring that you have a comprehensive understanding of these vital components.
What Are Flare Nuts?
Flare nuts, also known as flare fittings, are specialized fasteners used primarily in plumbing and automotive applications. They are characterized by their conical shape, which allows them to create a tight seal when connected to a corresponding flare fitting. The design of flare nuts is specifically engineered to handle high-pressure situations, making them ideal for use in hydraulic systems, fuel lines, and other critical applications.
The primary function of a flare nut is to secure a pipe or tube to a fitting, ensuring that no leaks occur during operation. The conical shape of the flare nut allows it to compress against the conical surface of the fitting, creating a seal that can withstand significant pressure. This design is particularly important in automotive applications where fuel and hydraulic fluid are transported under high pressure.
Flare nuts are typically made from materials such as brass, stainless steel, or aluminum, each offering unique benefits. Brass is known for its excellent corrosion resistance and machinability, making it a popular choice for plumbing applications. Stainless steel, on the other hand, is preferred in environments where high strength and resistance to extreme temperatures are required. Aluminum is lightweight and often used in applications where weight savings are essential.
Another important aspect of flare nuts is their threading. The threads on a flare nut must match those of the fitting to ensure a secure connection. There are various thread standards, including NPT (National Pipe Thread) and AN (Army-Navy), which must be considered when selecting the appropriate flare nut for a specific application.
In summary, flare nuts are essential components that facilitate the secure connection of pipes and tubes in a variety of applications. Their unique design, material options, and threading variations make them versatile and reliable components in both plumbing and automotive systems.
Types of Flare Nuts
Flare nuts come in various types, each designed for specific applications and requirements. Understanding these types can help you choose the right flare nut for your project, ensuring optimal performance and reliability.
One common type of flare nut is the 45-degree flare nut, which is widely used in plumbing and hydraulic applications. This design features a 45-degree angle on the flare, allowing for a smooth and effective sealing surface. This type is particularly popular in fuel lines and refrigeration systems, where a secure connection is vital to prevent leaks.
Another type is the 37-degree flare nut, commonly found in aerospace and automotive applications. This design features a sharper angle, which allows for a tighter fit and enhanced sealing capabilities. The 37-degree flare is often used in high-pressure applications, such as fuel and hydraulic lines, where safety and reliability are paramount.
In addition to these standard types, flare nuts are also available in various sizes and thread configurations. This allows for flexibility in applications, ensuring that the correct nut can be selected for the specific pipe or tube diameter and fitting type. Whether you are working with small plumbing systems or large automotive assemblies, there is likely a flare nut designed to meet your needs.
* * *
Take a look around on Temu, which delivers your order to your doorstep very quickly. Click on this link: https://temu.to/m/uu4m9ar76ng and get a coupon package worth $100 on Temu, or enter this coupon code: acj458943 in the Temu app and get 30% off your first order!
* * *
Moreover, some flare nuts come with additional features, such as knurled or smooth surfaces for improved grip during installation. These design variations can enhance the ease of use and the overall effectiveness of the flare nut in specific applications.
Understanding the different types of flare nuts available and their specific uses is essential for anyone involved in plumbing or automotive work. By selecting the appropriate flare nut for your application, you can ensure a secure and leak-free connection that will stand the test of time.
Applications of Flare Nuts
Flare nuts are utilized across a wide range of industries, from plumbing to automotive, due to their reliable sealing capabilities and ability to handle high-pressure situations. Understanding the various applications of flare nuts can help you appreciate their importance and versatility.
In plumbing, flare nuts are commonly used to connect copper or aluminum tubing to fittings. They are often found in refrigeration lines, where they help create a tight seal that prevents refrigerant leaks. This is crucial for maintaining the efficiency of refrigeration systems and ensuring that they operate safely.
In automotive applications, flare nuts play a vital role in connecting fuel lines and hydraulic systems. For instance, they are often used to secure brake lines, ensuring that hydraulic fluid is contained within the system and does not leak. This is essential for the safe operation of vehicles, as any loss of hydraulic fluid can lead to brake failure.
Additionally, flare nuts are used in pneumatic systems to connect air lines and fittings. Their ability to provide a secure and leak-free connection makes them ideal for applications where compressed air is used, such as in air tools and pneumatic machinery.
The aerospace industry also relies on flare nuts for high-pressure applications, where safety and reliability are critical. Flare nuts are used to connect fuel lines and hydraulic systems in aircraft, ensuring that these systems operate efficiently and safely at high altitudes and varying temperatures.
In summary, the applications of flare nuts are diverse and essential across multiple industries. Their ability to create secure, leak-free connections in high-pressure environments makes them indispensable components in plumbing, automotive, aerospace, and pneumatic systems.
Best Practices for Installing Flare Nuts
Proper installation of flare nuts is essential for ensuring their effectiveness and preventing leaks. Following best practices during installation can help you achieve a secure connection and extend the lifespan of your plumbing or automotive system.
First and foremost, it is crucial to select the correct size and type of flare nut for your specific application. Ensure that the threading matches the fitting and that the flare angle is appropriate for the connection. Using the wrong size or type of flare nut can lead to leaks and potential system failures.
Before installation, inspect the flare nut and the mating surfaces for any signs of damage or debris. Clean both surfaces thoroughly to ensure a tight seal. Any dirt, grease, or imperfections can compromise the effectiveness of the connection, leading to leaks.
When installing the flare nut, hand-tighten it first to ensure proper alignment. Once it is snug, use a wrench to tighten it further. However, be cautious not to overtighten the flare nut, as this can lead to crushing the fitting or damaging the threads. A good rule of thumb is to apply enough torque to create a seal without overexerting pressure.
After installation, it’s advisable to conduct a pressure test to check for leaks. This can be done by applying pressure to the system and visually inspecting the connection for any signs of fluid or gas escaping. If you notice any leaks, it’s essential to address them immediately, either by tightening the flare nut or re-evaluating the installation.
In conclusion, following best practices for installing flare nuts can significantly enhance the reliability and performance of your plumbing or automotive systems. By selecting the right components, ensuring cleanliness, and applying proper torque, you can create secure and effective connections that stand the test of time.
In any case, if you encounter issues or have concerns about your installation, consulting with a professional or a specialized technician can provide valuable insights and ensure that your systems operate safely and efficiently.

