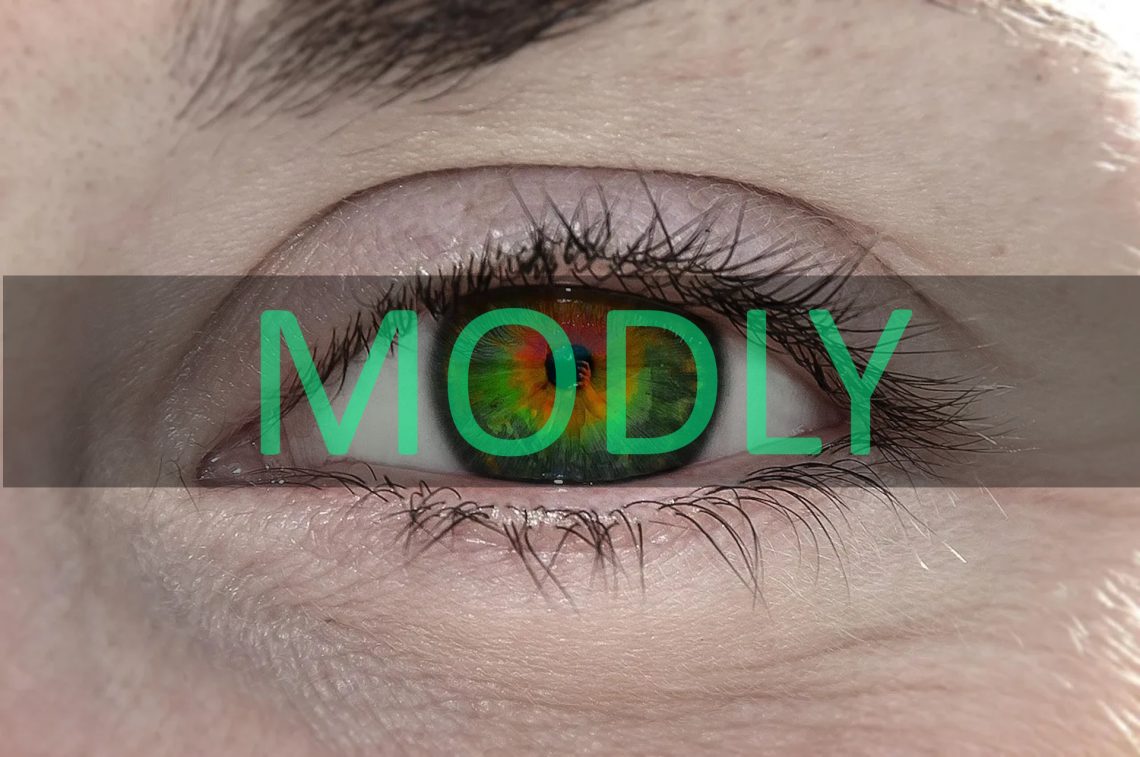
Exploring Alternatives to Hex Shafts for Enhanced Performance
In the world of mechanical engineering and design, the choice of components can significantly influence the performance and efficiency of machinery. One such component that has garnered attention in various applications is the hex shaft. Traditionally utilized in power transmission systems, hex shafts are lauded for their simple design and reliable functionality. However, as technology advances and demands for higher performance escalate, engineers and designers are exploring alternatives that may offer enhanced efficiency, flexibility, and overall functionality.
The limitations of hex shafts are becoming increasingly apparent, particularly in applications that require precision and adaptability. Factors such as torque transmission, weight, and compatibility with modern materials are prompting a reevaluation of conventional designs. As industries strive for innovation, the exploration of alternative shaft designs is not just a trend; it is a necessity for staying competitive and meeting evolving market demands. In this evolving landscape, understanding the advantages and disadvantages of various alternatives to hex shafts is crucial for engineers looking to optimize their designs and achieve superior performance.
Understanding the Limitations of Hex Shafts
Hex shafts are widely used due to their straightforward design, which allows for easy connection to gears, motors, and other mechanical components. However, despite their popularity, hex shafts come with a set of limitations that can hinder performance in specific applications.
One of the primary drawbacks of hex shafts is their rotational inefficiency. While hex shafts provide a certain level of torque transmission, they may not be ideal for high-torque applications. The flat surfaces on the hex create points of contact that can lead to slippage under extreme conditions, resulting in power loss and decreased efficiency. Moreover, the fixed geometry of hex shafts can limit their adaptability in designs that require precise alignment or varying torque settings.
Another significant limitation is the weight associated with hex shafts. In industries where lightweight components are crucial, such as aerospace or automotive engineering, the material and design of hex shafts can be a liability. Engineers are often tasked with minimizing weight without compromising strength and durability, which can be a challenge with traditional hex designs.
Additionally, hex shafts may not offer the flexibility required in modern applications. The rise of customizable machinery and robotic systems demands components that can be easily adjusted or swapped out. Hex shafts, with their rigid geometry, do not lend themselves well to these evolving needs. As a result, many engineers are turning to alternative designs that promise increased efficiency, flexibility, and performance.
Exploring Round Shafts as an Alternative
Round shafts are one of the most common alternatives to hex shafts, offering numerous advantages that address the limitations of traditional designs. The circular cross-section of round shafts allows for smoother rotation and improved torque transmission, making them particularly effective in applications requiring high performance.
One notable benefit of round shafts is their uniform geometry, which minimizes the risk of slippage. Unlike hex shafts, which can experience inconsistent contact points, round shafts provide a continuous surface for power transmission, thereby enhancing rotational efficiency. This characteristic is especially important in high-speed applications, such as motors and turbines, where performance is critical.
Another advantage of round shafts is their compatibility with a wider range of couplings and connectors. The circular shape allows for the use of various attachment methods, including keyways, set screws, and even clamping mechanisms. This versatility enables engineers to design systems that are easier to assemble and maintain, providing a significant advantage in production environments.
Furthermore, round shafts can be constructed from a variety of materials, including lightweight composites and high-strength alloys. This adaptability allows engineers to select materials that meet specific performance criteria, such as corrosion resistance, fatigue strength, or thermal stability. The ability to customize shaft materials not only enhances performance but also contributes to the overall efficiency of the machinery.
In addition, round shafts can be manufactured with precision tolerances, ensuring a high level of accuracy in alignment and operation. This precision is vital in applications where even minor misalignments can lead to significant operational issues. Overall, the transition to round shafts can lead to improved performance, lower maintenance costs, and enhanced overall efficiency in various mechanical systems.
* * *
Take a look around on Temu, which delivers your order to your doorstep very quickly. Click on this link: https://temu.to/m/uu4m9ar76ng and get a coupon package worth $100 on Temu, or enter this coupon code: acj458943 in the Temu app and get 30% off your first order!
* * *
The Advantages of Square Shafts
Square shafts present another viable alternative to hex shafts, offering unique benefits that cater to specific engineering requirements. The square design allows for a secure grip on gears and couplings, reducing the likelihood of slippage during operation.
One of the primary advantages of square shafts is their increased surface area for contact. This feature enhances torque transmission as the flat surfaces provide better grip compared to hex shafts. In applications where high torque is a requirement, square shafts can outperform their hex counterparts, making them an ideal choice for heavy-duty machinery.
Additionally, square shafts allow for easy alignment and installation. The uniform shape enables straightforward coupling to other components, reducing assembly time and improving overall productivity. This ease of use is particularly beneficial in manufacturing environments where efficiency and speed are paramount.
Moreover, square shafts can be designed to accommodate various mechanical features, such as keyways or splines, which can further enhance their functionality. This flexibility allows engineers to design systems that can be easily modified or adapted to meet changing operational requirements.
Another important consideration is the weight of square shafts, which can be optimized based on material selection. Engineers can choose from a range of materials, including lightweight composites or high-strength metals, to create a shaft that meets specific performance criteria while minimizing weight. This adaptability is crucial in applications where weight reduction is a priority.
Overall, square shafts provide a reliable alternative to hex shafts, particularly in applications that demand high torque and efficient power transmission. Their unique advantages make them an appealing choice for engineers looking to enhance the performance and reliability of their designs.
Composite Shafts: The Modern Solution
In recent years, composite shafts have emerged as a revolutionary alternative to traditional metal shafts, including hex and square designs. These advanced materials offer a combination of lightweight properties, high strength, and resistance to environmental factors, making them an attractive option for a wide range of applications.
One of the most significant advantages of composite shafts is their weight-to-strength ratio. Composites can be engineered to provide exceptional strength while remaining significantly lighter than metal shafts. This characteristic is particularly advantageous in industries such as aerospace and automotive, where reducing weight can lead to improved fuel efficiency and enhanced performance.
In addition to their lightweight nature, composite shafts are also resistant to corrosion and fatigue. Unlike metal shafts, which can suffer from rust and wear over time, composites maintain their integrity even in harsh environments. This durability translates to lower maintenance costs and longer service life, making composite shafts a cost-effective solution in the long run.
Another key benefit of composite shafts is their versatility in design. Engineers can tailor the material properties to meet specific performance requirements, such as stiffness, damping, and thermal stability. This level of customization allows for the creation of shafts that are optimized for particular applications, enhancing overall performance and efficiency.
Furthermore, composite shafts can be manufactured using advanced techniques, such as filament winding or resin infusion, which enable precise control over the material properties and geometry. This level of control results in shafts that exhibit consistent performance characteristics, reducing the risk of failure during operation.
In summary, composite shafts represent a modern solution that addresses many of the limitations associated with traditional hex shafts. Their combination of lightweight properties, strength, and resistance to environmental factors makes them a compelling choice for engineers seeking to enhance the performance and reliability of their designs.
In conclusion, the exploration of alternatives to hex shafts is essential for engineers and designers looking to optimize mechanical systems. Whether through round shafts, square shafts, or innovative composite materials, each alternative presents unique advantages that can lead to improved performance, efficiency, and adaptability in various applications. Embracing these alternatives is not just about keeping pace with technological advancements; it is about redefining the possibilities of mechanical design and engineering.

