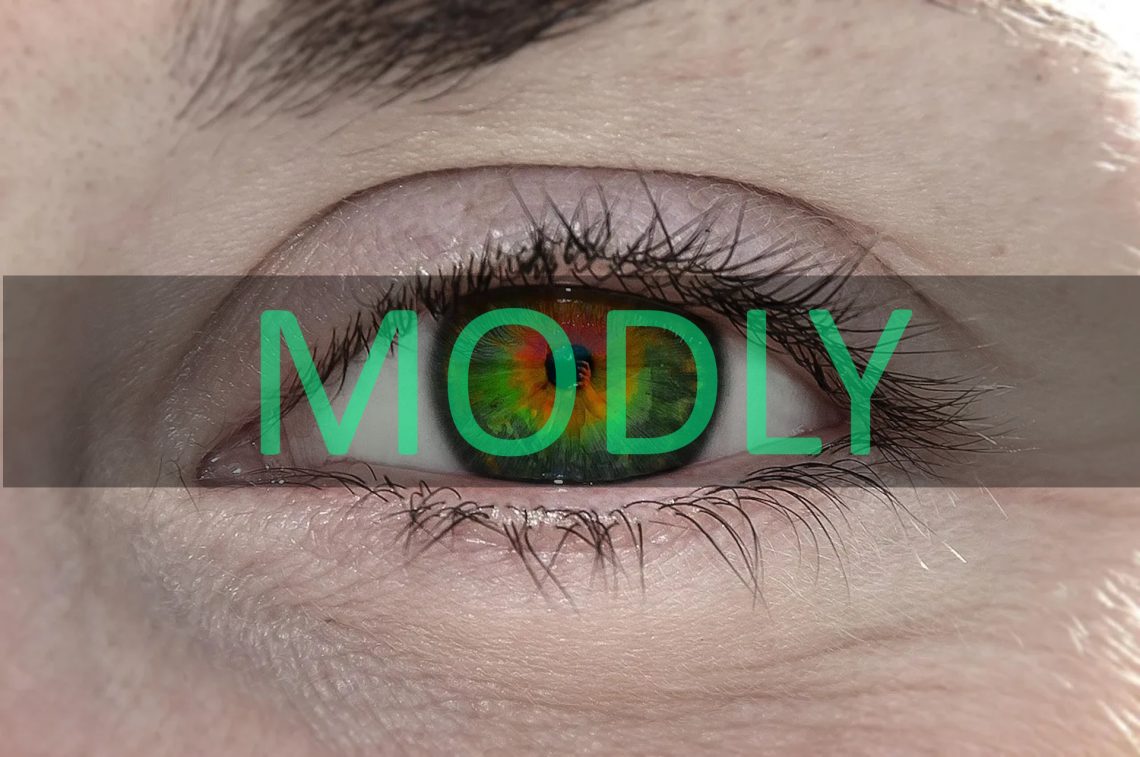
Exploring the Versatility and Use Cases of Cone Plates in Industry
In the ever-evolving landscape of industrial applications, the significance of specialized components cannot be overstated. Among these components, cone plates stand out for their unique design and functionality. These precision-engineered devices are integral to various processes, providing versatility that caters to a wide range of industry needs. Their shape and design allow for optimal performance in applications ranging from food processing to pharmaceuticals, and even in the automotive sector.
Cone plates are designed to facilitate specific functions, including mixing, emulsifying, and measuring properties of materials. Their geometry enables uniform shear rates and enhanced material flow, which is crucial for achieving consistent product quality. As industries strive for efficiency and reliability, the adoption of cone plates has become more prevalent. This trend is fueled by the demand for higher precision in manufacturing processes and the need to adhere to stringent quality standards.
The adaptability of cone plates has made them a valuable asset in both research and industrial settings. Understanding their applications and benefits can provide insights into how they can improve processes and outcomes across various sectors. As we delve deeper into the subject, we will uncover the multifaceted roles that cone plates play in different industries and highlight their significance in enhancing operational efficiency.
Understanding the Design and Functionality of Cone Plates
The design of cone plates is a fundamental aspect of their functionality. Typically composed of two conical surfaces, a cone plate setup allows for a unique flow pattern that is crucial for many industrial applications. The angle of the cone and the gap between the plates determine the shear rate experienced by the material being processed. This design is particularly beneficial when working with non-Newtonian fluids, where the viscosity can change under different shear rates.
One of the primary functions of cone plates is to create a uniform shear environment. This is especially important in applications such as mixing and emulsification, where consistent shear is required to achieve homogeneity. The geometry of cone plates ensures that materials are subjected to the same shear conditions regardless of their position within the system, leading to improved consistency in the final product.
In addition to their mixing capabilities, cone plates are also used in rheological testing. By measuring the flow behavior of materials under controlled shear conditions, manufacturers can gain valuable insights into their properties. This information is critical for product development, quality control, and ensuring that materials perform as expected in their intended applications.
Moreover, the ease of cleaning and maintenance of cone plates makes them a practical choice for industries that require strict hygiene standards, such as food and pharmaceuticals. Their smooth surfaces minimize the risk of contamination and facilitate thorough cleaning, ensuring compliance with regulatory requirements.
Overall, the design and functionality of cone plates make them an indispensable tool in various industrial settings, enabling better process control and product quality.
Applications of Cone Plates in Food Processing
In the food processing industry, the role of cone plates cannot be underestimated. They are widely used for emulsification, mixing, and texture modification. For instance, in the production of sauces and dressings, cone plates facilitate the even dispersion of oil and water phases, resulting in stable emulsions. The ability to achieve a consistent texture and flavor profile is essential in maintaining product quality and consumer satisfaction.
Cone plates are also employed in the production of dairy products, such as yogurt and cheese. During these processes, the controlled shear environment created by cone plates helps to ensure uniformity in product consistency and flavor. In addition, the design of cone plates allows for the efficient incorporation of ingredients, reducing processing times and improving overall efficiency.
Another significant application of cone plates in the food industry is in the analysis of rheological properties. Understanding the flow behavior of food products is crucial for predicting their performance during processing and storage. By using cone plates for rheological testing, manufacturers can optimize formulations and processing conditions, ultimately leading to better product outcomes.
Furthermore, the versatility of cone plates extends to the production of beverages, where they are used for mixing and homogenization. In the beverage industry, achieving a uniform product is vital for consumer acceptance. Cone plates enable manufacturers to create consistent flavor profiles and textures, ensuring that every sip meets consumer expectations.
* * *
Take a look around on Temu, which delivers your order to your doorstep very quickly. Click on this link: https://temu.to/m/uu4m9ar76ng and get a coupon package worth $100 on Temu, or enter this coupon code: acj458943 in the Temu app and get 30% off your first order!
* * *
In summary, cone plates play a pivotal role in food processing, enhancing product quality, consistency, and efficiency. Their unique design and functionality make them an essential component in the manufacturing of a wide range of food products.
The Role of Cone Plates in Pharmaceutical Manufacturing
In the pharmaceutical industry, the precision and reliability of manufacturing processes are paramount. Cone plates are increasingly being utilized for their ability to provide consistent shear and mixing, which are critical for ensuring the efficacy and safety of pharmaceutical products. These devices are particularly valuable in the production of suspensions, emulsions, and other complex formulations.
One of the key advantages of using cone plates in pharmaceutical manufacturing is their ability to create uniform mixtures. In the formulation of medications, it is crucial that active ingredients are evenly distributed throughout the product. Cone plates facilitate this process by providing a controlled shear environment that promotes thorough mixing without introducing excessive air, which could compromise product stability.
Moreover, cone plates are instrumental in the development of drug delivery systems. The rheological properties of these systems must be carefully controlled to ensure that they perform as intended within the body. By utilizing cone plates for rheological testing, pharmaceutical manufacturers can assess the flow behavior of their formulations and make necessary adjustments to optimize performance.
In addition to their mixing capabilities, cone plates are also used in the characterization of materials. Understanding the flow and viscosity properties of raw materials is essential for ensuring that they meet the required specifications for pharmaceutical applications. Cone plates provide a reliable method for evaluating these properties, enabling manufacturers to make informed decisions about their formulations.
Furthermore, the easy cleaning and sanitization of cone plates make them a suitable choice for environments where hygiene is critical. In pharmaceutical manufacturing, maintaining strict cleanliness standards is essential to prevent contamination and ensure product safety.
Overall, the integration of cone plates into pharmaceutical manufacturing processes enhances product quality and consistency while streamlining operations.
Innovations and Future Trends in Cone Plate Technology
As industries continue to evolve, so too does the technology surrounding cone plates. Innovations in materials, design, and manufacturing processes are driving advancements that enhance the functionality and versatility of these essential components. One notable trend is the development of cone plates made from advanced materials that offer improved durability and resistance to wear and chemical exposure. This innovation extends the lifespan of cone plates and reduces the need for frequent replacements, ultimately leading to cost savings for manufacturers.
Additionally, the integration of smart technology into cone plate systems is becoming increasingly prevalent. Sensors and monitoring systems can provide real-time data on shear rates, temperature, and viscosity, allowing manufacturers to optimize processes and improve product quality. This level of control and data-driven decision-making is transforming the way industries operate, making them more efficient and responsive to changing market demands.
Another area of innovation is the customization of cone plates for specific applications. Manufacturers are increasingly recognizing the importance of tailored solutions that meet the unique needs of their processes. This trend is leading to the development of cone plates with adjustable angles, sizes, and surface textures, providing greater flexibility in their use across various industries.
Moreover, as sustainability becomes a focal point for many industries, the design of cone plates is also shifting towards more environmentally friendly practices. The use of recyclable materials and energy-efficient manufacturing processes is gaining traction, aligning with the broader goals of reducing waste and minimizing environmental impact.
In conclusion, the future of cone plate technology is poised for exciting advancements that will further enhance their versatility and applications in various industries. As manufacturers continue to seek efficiency and quality, the role of cone plates will remain critical in achieving these objectives.
**Disclaimer:** This article is not intended as medical advice. For any health-related concerns, please consult a qualified healthcare professional.

