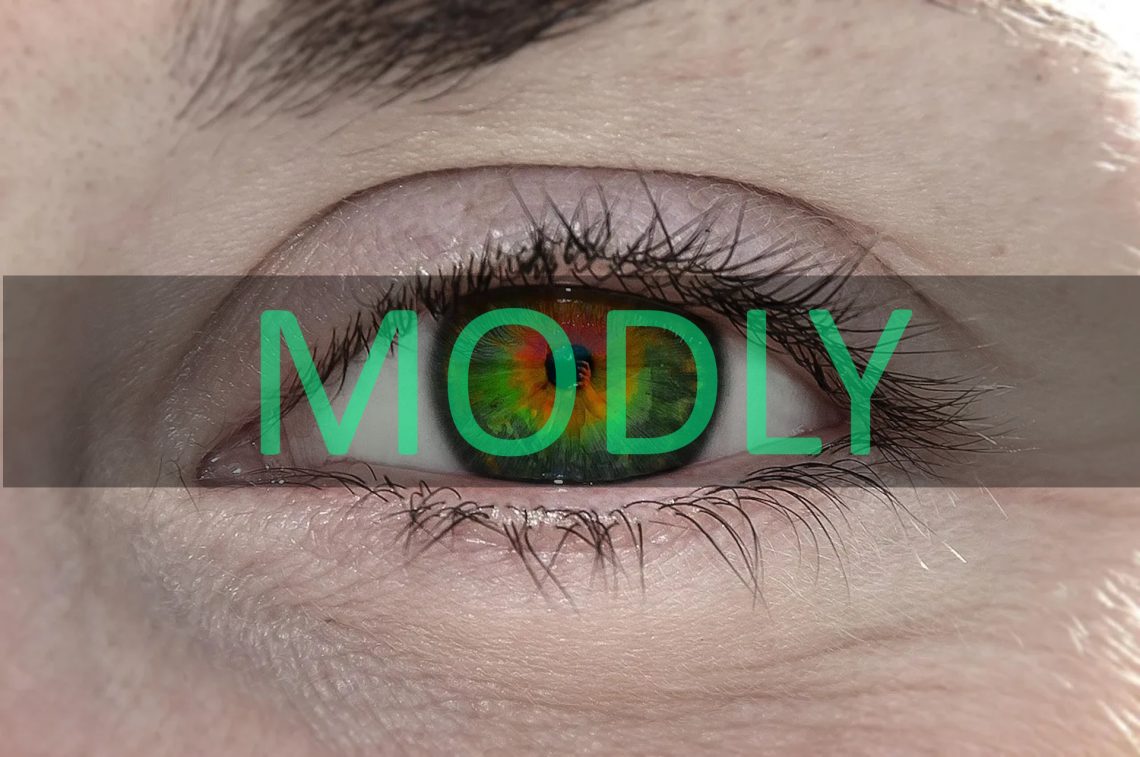
Understanding the Bend Test for Rib Structural Integrity
Understanding the Bend Test for Rib Structural Integrity
In the realm of structural engineering and materials testing, ensuring the integrity of components is paramount. One crucial aspect of this process involves testing the strength and durability of materials used in various applications. Among these tests, the bend test stands out as a reliable method for assessing the performance of structural elements, particularly ribs in various constructions. The bend test provides vital insights into how materials behave under stress, revealing their ability to withstand loads without failure.
This method is particularly important in industries such as automotive, aerospace, and construction, where structural integrity directly impacts safety and performance. Ribs, being integral to the overall design, play a significant role in distributing loads and maintaining stability. A thorough understanding of how these components respond to bending forces is essential for engineers and designers alike. The bend test not only aids in material selection but also in quality control during the manufacturing process. As we delve deeper into the mechanics of the bend test, we will uncover its significance, methodologies, and implications for ensuring structural integrity.
The Importance of the Bend Test in Structural Engineering
The bend test holds a central position within the framework of structural engineering, especially concerning the evaluation of rib components. This test is vital for determining a material’s ability to withstand bending stresses without succumbing to deformation or failure. In structural applications, ribs serve to enhance the strength of a framework, making it essential to evaluate their performance accurately.
One of the primary reasons for conducting a bend test is to assess the ductility and toughness of materials. Ductility refers to a material’s capacity to deform under stress, while toughness indicates its ability to absorb energy and resist fracture. By applying a controlled bending force, engineers can observe how a rib reacts, providing critical data on its mechanical properties. This information is crucial when selecting materials for specific applications, as it ensures that the chosen components can endure the anticipated loads.
Moreover, the bend test plays a significant role in quality assurance during manufacturing processes. By routinely testing samples from production batches, manufacturers can identify any deviations in material properties that may arise due to inconsistencies in the manufacturing process. Early detection of such issues can prevent potential failures in the field, ultimately enhancing safety and reliability.
Additionally, the bend test is not limited to a single type of material; it can be applied to a wide range of substances, including metals, polymers, and composites. This versatility makes it an invaluable tool across various industries. The outcomes of the bend test inform engineers about the limits of each material, enabling them to make informed decisions regarding design specifications and safety margins.
In summary, the bend test is a fundamental procedure in structural engineering that provides essential insights into the performance and reliability of rib components. Its ability to gauge ductility, toughness, and manufacturing consistency makes it an indispensable part of the engineering landscape.
Methodologies of the Bend Test
Conducting a bend test involves several methodologies, each tailored to meet specific requirements based on the material being tested and the desired outcomes. The most common methodologies include the three-point bend test, four-point bend test, and the cantilever bend test. Each of these methods offers unique advantages and insights into material behavior.
The three-point bend test is one of the most widely used techniques. In this method, a sample is placed on two supports, and a load is applied at the midpoint. This configuration allows for the measurement of the material’s flexural strength and modulus of elasticity. The simplicity of the setup and the straightforward analysis of results make the three-point bend test a favorite among engineers.
On the other hand, the four-point bend test provides a more uniform distribution of stress across the sample. In this setup, two loads are applied at two points along the span of the sample, which helps to minimize the effects of stress concentration at the center. This method is particularly useful for materials that exhibit nonlinear behavior or those that require a more detailed analysis of their mechanical properties.
The cantilever bend test is another approach, particularly suited for materials that are often used in beam applications. In this configuration, one end of the sample is fixed while a load is applied to the free end. This setup mimics real-world applications more closely and provides insights into how materials behave under practical loading conditions.
* * *
Take a look around on Temu, which delivers your order to your doorstep very quickly. Click on this link: https://temu.to/m/uu4m9ar76ng and get a coupon package worth $100 on Temu, or enter this coupon code: acj458943 in the Temu app and get 30% off your first order!
* * *
Regardless of the method used, it is essential to follow standardized procedures to ensure the reliability and repeatability of results. This includes adhering to specific dimensions, loading rates, and environmental conditions during testing. By maintaining consistency in testing parameters, engineers can compare results across different studies and materials effectively.
In conclusion, the methodologies of the bend test are diverse and adaptable, providing engineers with critical insights into the structural integrity of materials. By selecting the appropriate testing method, professionals can ensure that their designs meet safety and performance standards.
Interpreting Bend Test Results
Interpreting the results of a bend test is a crucial step in evaluating material performance and structural integrity. The data obtained from the test provides key indicators of a material’s mechanical properties, such as flexural strength, modulus of elasticity, and failure modes. Understanding these metrics is essential for engineers during the design and analysis phases.
Flexural strength is one of the primary outcomes of a bend test, indicating the maximum stress a material can withstand before failure. This value is typically expressed in megapascals (MPa) or pounds per square inch (psi). A higher flexural strength signifies that the material can endure greater loads without deforming, which is especially important for structural applications where safety is a concern.
The modulus of elasticity, another critical parameter derived from bend testing, reflects the material’s stiffness. It quantifies how much a material will deform under a given load. A higher modulus indicates a stiffer material, which may be desirable in certain applications where rigidity is essential. Conversely, materials with lower moduli may be more suitable for applications where flexibility and resilience are required.
In addition to these quantitative results, the bend test also provides qualitative insights into the material’s behavior during loading. Observing the failure mode—whether it is a clean break, bending without fracture, or yielding—can offer valuable information about the material’s properties. For instance, a material that exhibits ductile failure may be more suitable for applications requiring energy absorption, while a brittle failure mode might indicate a need for caution in design.
Furthermore, comparing bend test results across different materials allows engineers to make informed decisions about material selection for specific applications. By understanding how various materials respond to bending forces, professionals can optimize designs for maximum performance and safety.
In summary, interpreting bend test results is a multifaceted process that provides essential information about material properties. By analyzing flexural strength, modulus of elasticity, and failure modes, engineers can ensure that their designs meet the necessary performance and safety standards.
Applications of the Bend Test in Various Industries
The applications of the bend test span a wide range of industries, reflecting its importance in ensuring structural integrity and safety. From aerospace to automotive and construction, this testing method provides critical insights that influence design and manufacturing decisions.
In the aerospace industry, where weight and strength are paramount, the bend test is essential for evaluating materials used in aircraft components. Engineers must ensure that materials can withstand the stresses encountered during flight, including turbulence and variations in pressure. The bend test helps identify materials that offer the best balance between lightweight properties and structural integrity, ensuring the safety and performance of aircraft.
Similarly, in the automotive sector, the bend test is crucial for assessing the strength of components such as chassis, frames, and suspension systems. These parts must endure significant loads and dynamic forces during operation. By conducting bend tests, manufacturers can identify materials that offer the necessary strength and durability, ultimately enhancing vehicle safety and performance.
The construction industry also heavily relies on the bend test to evaluate materials used in beams, columns, and other structural elements. Building codes often specify minimum strength requirements for materials, and conducting bend tests ensures compliance with these standards. This testing not only helps in selecting suitable materials but also plays a vital role in quality control during the construction process.
Moreover, the bend test is increasingly relevant in the field of advanced materials, such as composites and polymers. As industries continue to innovate and develop new materials, understanding their mechanical properties through bend testing becomes essential for their successful application.
In conclusion, the bend test is a pivotal procedure across various industries, providing essential data that informs material selection and design decisions. Its role in ensuring safety and structural integrity cannot be overstated, making it a critical component of engineering practices.
This article does not constitute medical advice. For any health-related issues, please consult a qualified healthcare professional.

